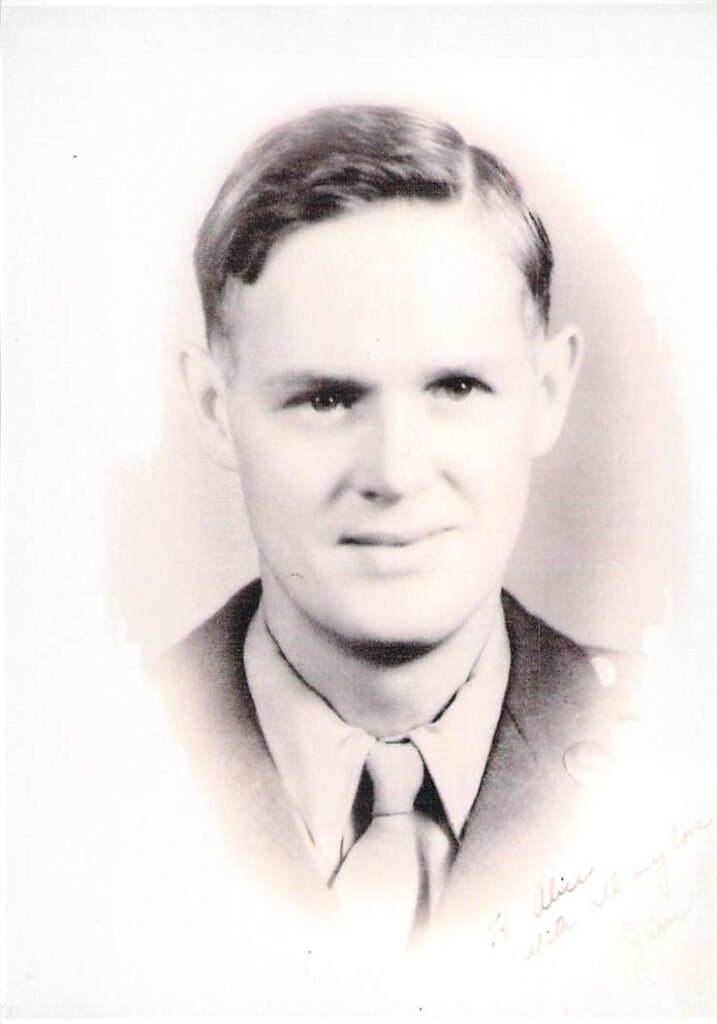
Thorndike Engineering founded by James O. Thorndike Sr. opened its doors in 1946 and began manufacturing intricate and often delicate microwave dielectrics. Many companies could produce individual pieces by hand, but were unable to produce with close tolerances in the numbers that the industry needed. The founder of Thorndike Engineering, James O. Thorndike Sr. took on the challenge of finding new methods of economically producing them in large quantities. He stated, “Never think of why it can’t be done, think only of how to do it.”
James O. Thorndike Jr. developed new and creative approaches to do the job. He came up with formulations for both Low and High power Polyiron TCXXXX series materials as well as our High Power TC4000HT (SiC) series materials which are both used in all areas of the industry.
Over the years and now a third-generation, James O. Thorndike III has continued to grow Thorndike Corporation’s methods of custom injection molding and complex casting abilities which has made us unique in the industry. This has made it possible for us to economically mass produce parts that other companies have said could not be produced in numbers at any price. For the past 75 plus years Thorndike Engineering / Corporation has been at the forefront of the microwave industry supplying military, aerospace, satellite, medical, commercial, industrial, wireless, telecom research and automotive fields. With over 38,000 different parts in our data base, and we continually design new parts, we’re sure to be your “one stop shop” for all your Microwave Absorbing, Low Loss Dielectrics and Electrically Conductive Shielding materials/loads.
Another significant factor in the success of Thorndike Corporation has been that we produce our own raw material from which the dielectrics are made. We produce our material in our own Raw Materials Lab using our own formulations. Our materials are used in high and low power applications and are used in many components such as terminations, attenuators, mode suppressors, EMI suppressors, filters, couplers, and virtually anywhere microwave suppression is desired. They can be prepared to meet the customer’s specific needs using any of our 105 plus standard formulations or any range between these formulas. Thorndike raw materials meet NASA aerospace criteria and can be milled, bored, threaded, tapped and ground. It is available in bars, rods, sheet stock and custom injection molding to exact customer dimensions, holding tolerances within .00001”.
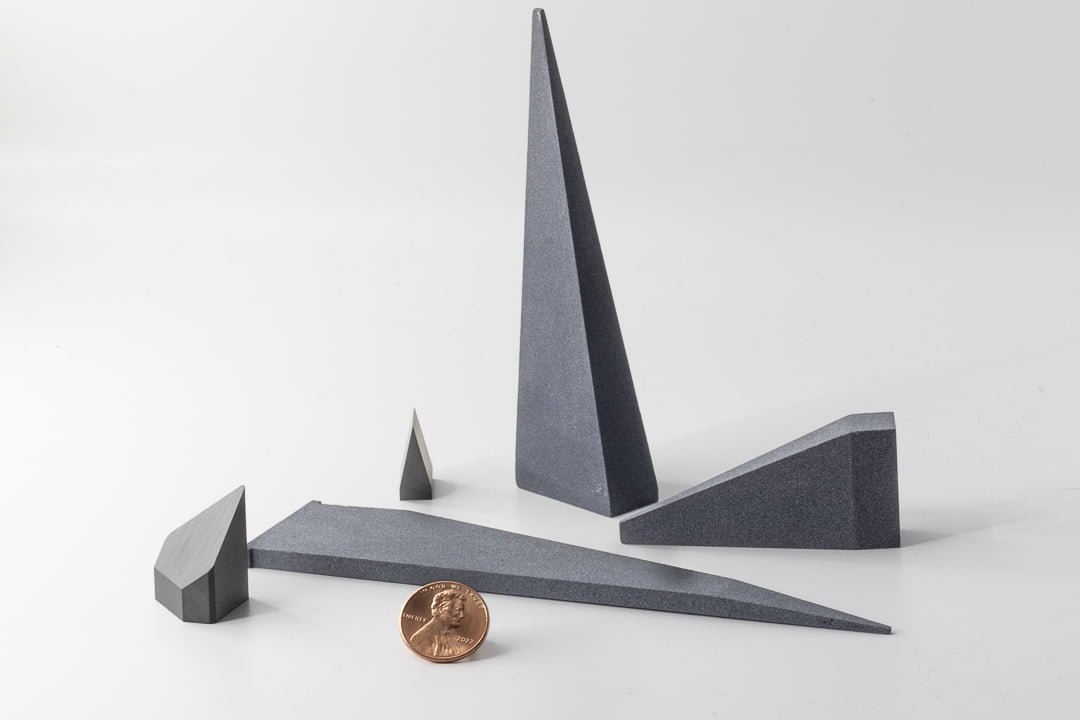
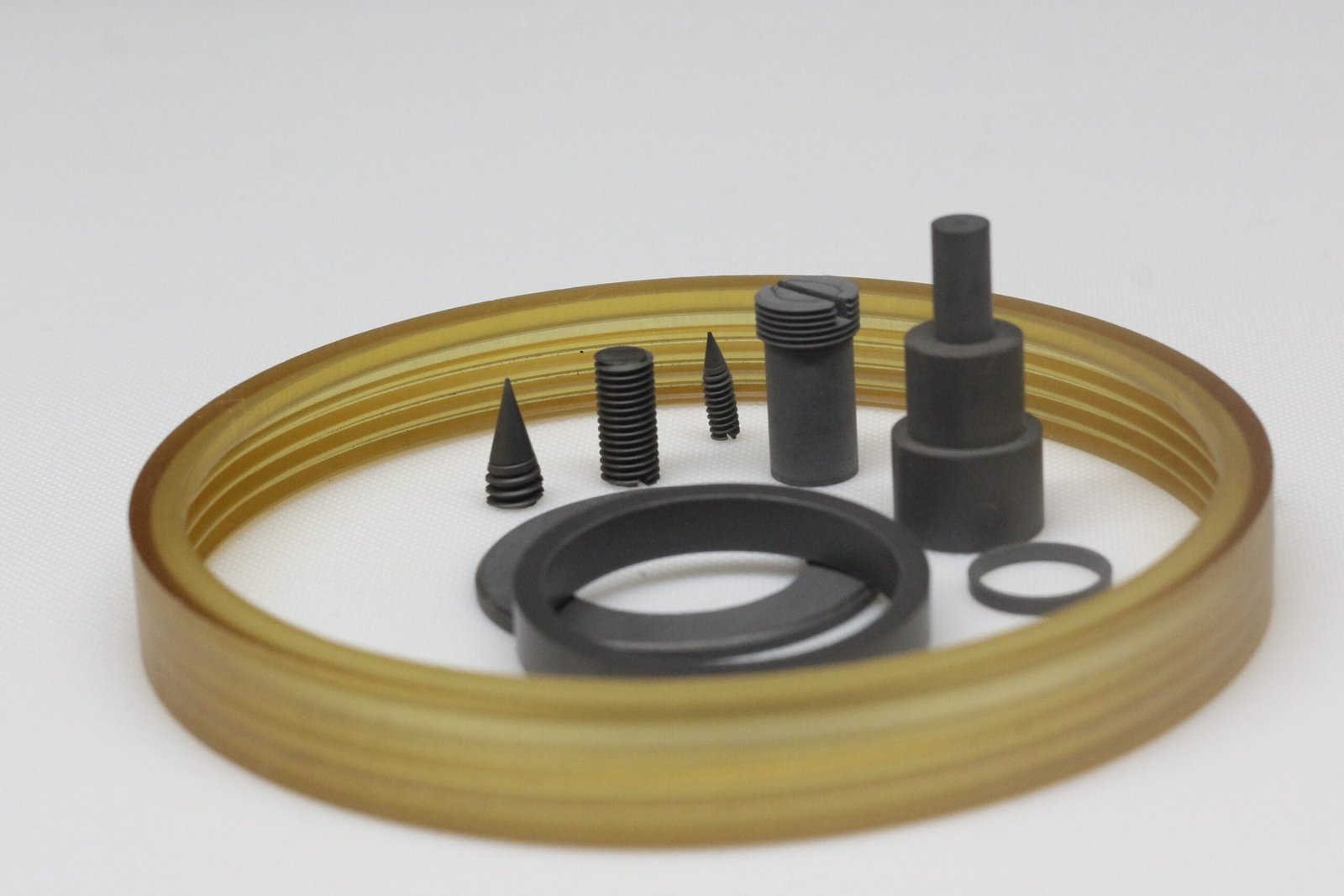
Thorndike Corporation is a leading design and precision manufacturer of microwave absorbing dielectrics supplying the military, commercial and industrial fields with 77 years of continuous service. We manufacture our own line of high loss absorbers to fit hundreds of old requirements and customize parts for new designs. Our current formulas include the exact equivalents to the old standard materials used in microwave applications over the past 50 plus years. Our materials are used in many components such as terminations, attenuators, mode suppressors, EMI suppressors, filters, couplers, and virtually anywhere microwave frequency suppression is desired.
Customers
Our customers range from large world-wide commercial industries, military and government institutions, scientific companies, to private and small leading-edge entrepreneurs.
We manufacture based on the customer’s needs; from a one-piece sample prototype and finished product to a production run exceeding one million pieces. For new designs, prototypes, or engineering upgrades, we provide the electrical and mechanical design for many types of microwave products, from system specifications.
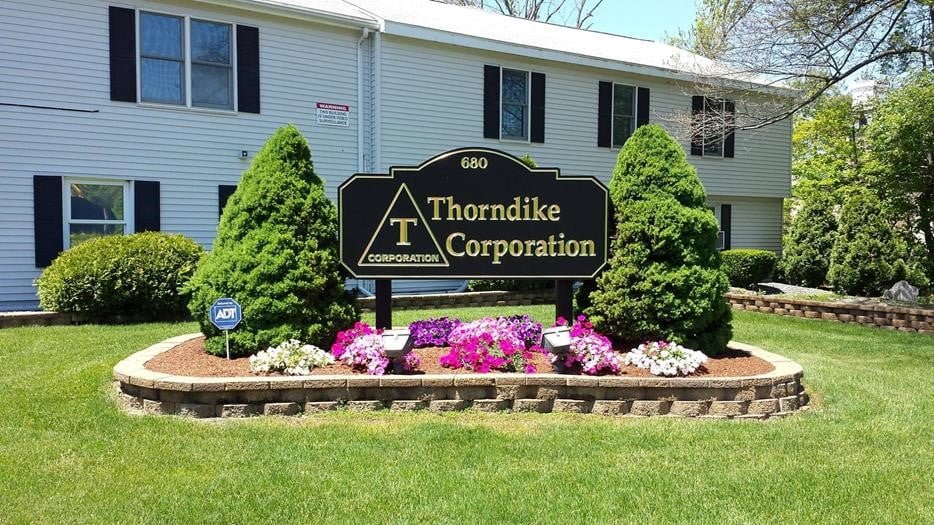
Machine Shop
The machining capabilities at Thorndike Corporation are extensive; many of which are housed on-site in our 18,000 sq. ft. facility.
At Thorndike Corporation we provide custom molding which allows us to eliminate excessive labor costs. This allows us to streamline the productions process and pass on these savings to our customers. In addition, we mold, machine, die cut and grind raw stock materials into precise engineering prototypes or full production runs. Our machine shop includes C.N.C. lathes, C.N.C. millers, lathes, millers, surface grinding, Blanchard grinding, 10 and 00 grinding and grinders capable of machine all types of dielectrics, plastics, and silicon carbide. We can also centerless grind rod stock to almost any length and diameter. Our machine shop manufactures to print, finished components using either our own materials or yours.
Engineering/Electrical Testing



Thorndike Corporation/Engineering designs and tests all of our components to meet our customers requirements. Thorndike Corporation employs Engineering Specialty Services (E.S.S) which is located on the second floor of our facility for all component design and development. Electrical testing which is also done by E.S.S is incorporated into our pricing so no additional expense for testing is required by our customers. We provide inspection and test data for our components to all our customers for review by the buyer. We therefore guarantee our parts to meet the electrical and mechanical requirements as quoted and will offer a full refund and return shipping at our expense if you find the parts do not meet our published specifications. We take great pride in making Thorndike Corporation a one stop shop for all our customers microwave requirements, from the manufacture of the dielectric materials, component design, manufacture and testing all-inclusive in our customer pricing.